When it comes to choices for siding for home construction, builders have quite a few to work with. The quality, workability and costs vary greatly, and the final choice is often determined by both the structural and weather-resistance needs of the project, and the builder’s budget.
When it comes to choices for siding for home construction, builders have quite a few to work with. The quality, workability and costs vary greatly, and the final choice is often determined by both the structural and weather-resistance needs of the project, and the builder’s budget.
On the high end of siding options, there is faux stone, brick and stone veneer, wood, fiber cement and engineered wood. At the least expensive end of the siding product spectrum is vinyl, stucco, aluminum and steel, and T1-11 and composite board, which fall roughly in the middle of the cost range.
The product we typically consider to be “traditional” hardboard siding is a relatively inexpensive material that is easy to install. Hardboard siding material is harder than wood siding, which makes a more durable, and it’s more flexible. In addition, it can cost between 25 percent to 50 percent more than vinyl but less costly than wood.
What’s Good About Hardboard Siding
Hardboard siding is a vastly improved product from the original hardboard siding product known popularly as Masonite. In fact, Masonite ceased production of their siding products almost 20 years ago although contractors and vendors still use the name in a generic fashion when referring to modern hardboard siding products.
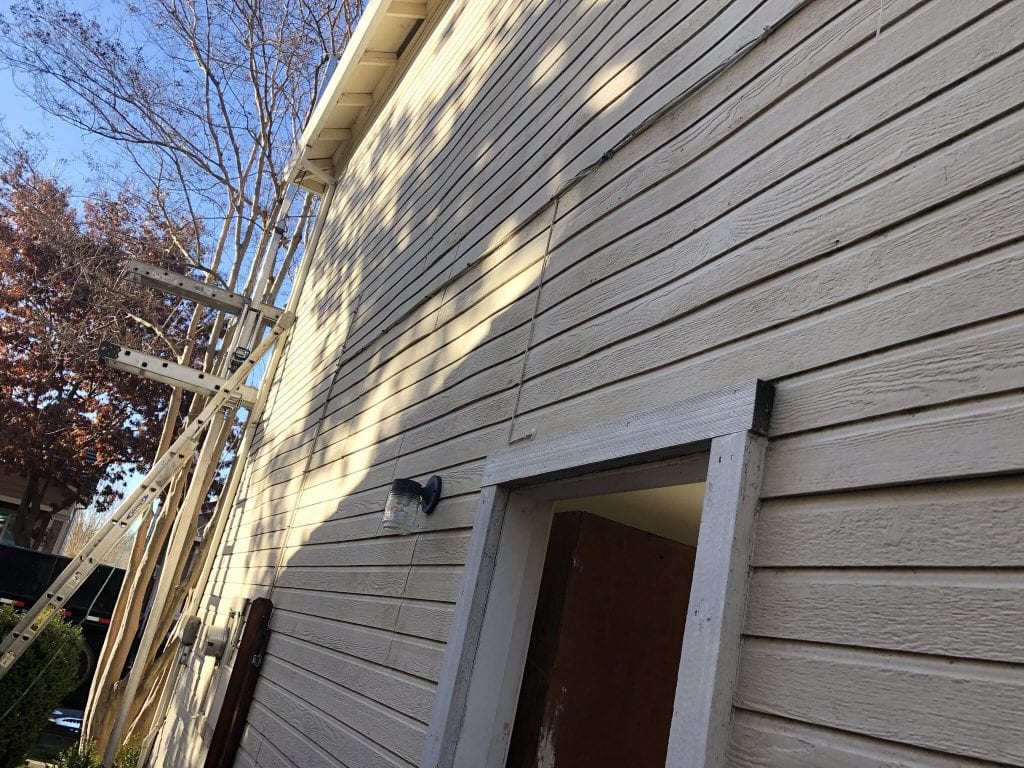
Despite the poor reputation that still lingers with hardboard, it has some good qualities. It can be painted in almost any color and the composite and surfaced plank board varieties resist the cracks and other surface issues typical with traditional wood.
Hardboard lap siding is also the easiest to install on homes that still have older style Masonite or clapboard siding that need small repairs.
The Problems with Hardboard Siding
First, we should go back and look at what happened to the “original” hardboard siding, Masonite. This product was invented in 1924 by William H. Mason. It was quite popular in the 1930s and 1940s and was used doors, roofing, and walls. After the Second World War, it was being used for residential siding.
Real problems for Masonite began in the 1970s and 1980s when some lines were not properly manufactured or sealed. This made the hardboard susceptible to mildew and rot, which caused expansion and contraction of the boards. In addition, poor and improper installation aggravated these issues.
In some cases, the boards rotted away where they were nailed to the house and the hardboard would fall off! As a result, in 1994, a nation-wide class-action suit was settled against some of the major hardboard siding products manufacturers. Masonite, which is a trademarked name, was not part of the suit.
The homeowners won the suit, which stipulated that specific owners of houses constructed using hardboard could be reimbursed for any damages caused by the product. As a result of the lawsuit, nearly all manufacturers stopped producing Masonite siding and, in March 2001, the Masonite Corporation announced its decision to phase out production of all hardboard siding products.
Today, similar “tempered hardboard” is now a generic product made by many forest product companies and is often, erroneously, referred to as Masonite.
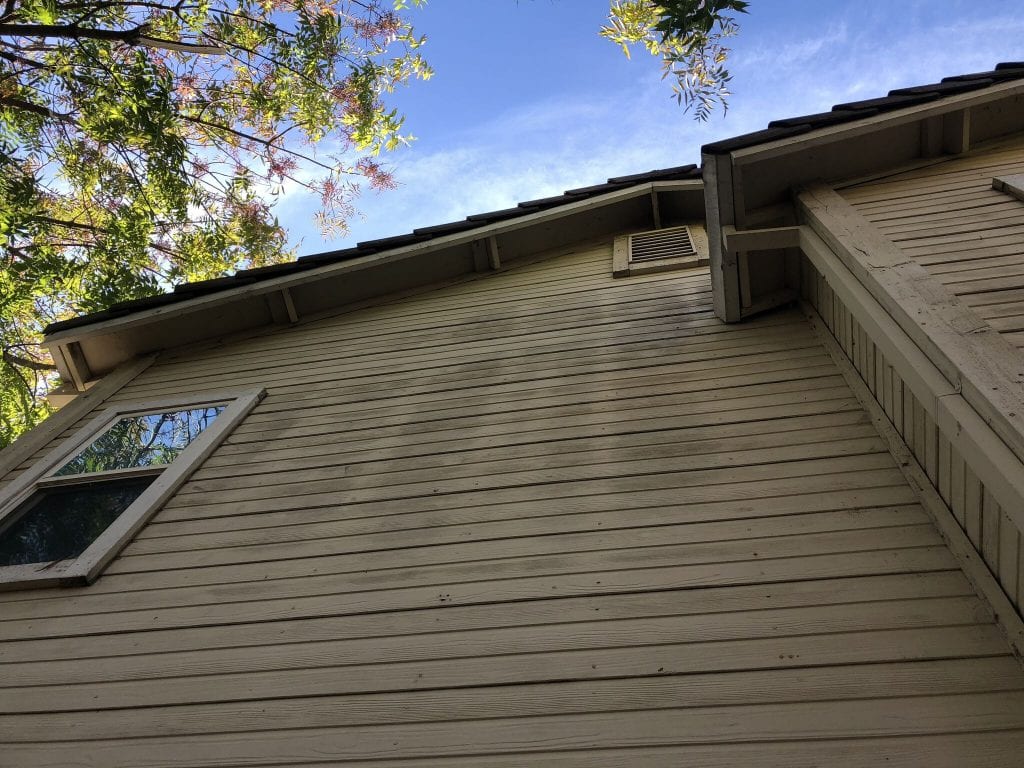
Modern hardboard siding products are far superior to the traditional materials. However, there are still some disadvantages to using a wood-based siding product. Panels that have been Improperly stained and sealed, for example, will allow moisture to make its way underneath the siding and cause mildew. In addition to product quality, improper installation can lead to moisture problems that can degrade the effectiveness and expose a house to mildew and moisture-related problems.
Even with the minor improvements made to hardboard siding, the most common problem we see with this siding type is installation error. Replacing hardboard siding represents nearly 50% of our siding sales and during our inspections we notice several common errors that builders made in the late 1980s and early 1990s. Builders would only install 1-2 “shear walls” with plywood under the siding and install the rest of the hardboard directly over the studs. The only siding that won’t warp or perform poorly when installed over studs is vertical siding that is 5/8” thick.
The biggest cause of dry rot in hardboard siding is inadequate water diversion flashing around gutter to siding transitions and installation of trim over the siding which does not allow for proper z-bar flashing over the head trim around windows. Furthermore, builders did not use joint connectors at the seams and would improperly nail the siding which would not allow the product to expand and contract and ultimately lead to bows in the siding. Lastly, homeowners failed to maintain this siding enough.
Those homeowners who painted their siding every 5-8 years and caulked around the trim would find their siding still standing today – those who did not have already installed new siding or need to right now. The most misleading aspect to the class-action lawsuit and general disdain for hardboard siding is that home builders should share the responsibility of the product failure. It is safe to say that builders who used this product were happy when the lawsuit was accepted.
Alternatives to Hardboard Siding
Two great alternative siding products to consider LP® SmartSide® engineered wood siding and James Hardie fiber cement siding.
LP® SmartSide® is a siding product composed of chipped Aspen wood combined with a specialized resin formula used as a binding agent along with zinc borate for a treating element along with a phenolic acid overlay. The result is a product that offers superior moisture protection and strength. It comes in longer lengths than Hardie Board, weighs less, and is less expensive to install since there are no special cutting tools required.
Hardie Board, by the way, is not the same product as “hardboard,” which is a dense and thin pressed particleboard typically made from wood. Hardie Board is a fiber cement product known available as a horizontal lap siding called HardiePlank®, and a vertical siding called HardiePanel®. These fiber cement siding products are created from a proprietary formula of Portland cement mixed with ground sand, cellulose fiber, and other additives. Because of its popularity it has become a veritable generic product and referred to as concrete siding, cement fiber siding, and even fiber cement cladding.